
Autonomous Passenger Boarding Bridge (PBB)
ENHANCING SAFETY AND PRECISION IN PASSENGER BOARDING
The latest upgrades to the Autonomous Passenger Boarding Bridge Docking System (PBB) by CLX Engineering includes advanced monitoring systems that enhance safety and operational precision. With encoders and lasers installed across key components, including the cab, bogie, and rotunda, PBBs now feature improved motion control and collision avoidance capabilities. Enhanced disconnect circuits ensure safety-rated stops upon detecting faults, while the integration of machine vision cameras facilitates smoother auto-leveling and automatic docking for a seamless boarding experience.
ADVANCED FEATURES FOR IMPROVED MONITORING AND CONTROL
The upgraded PBB comes equipped with IoT sensors that monitor temperatures, vibrations, and positions in real-time, providing comprehensive data for maintenance and operation. The updated Human-Machine Interface (HMI) offers more control options, ensuring maintenance personnel have the tools they need for efficient operation. Additionally, SafeGate and AHU/PCAir interfaces now offer detailed insights into the timing of aircraft parking relative to power and air connection.
IoT Monitoring: Real-time sensors track temperatures, vibrations, distances, and rotational positions to ensure optimal performance.
Enhanced HMI: Updated operator interface provides more control options, improving maintenance and overall monitoring capabilities.
SafeGate Integration: Seamlessly interfaces with Gatebox and AHU/PCAir systems to monitor and report on power and air connections to the plane.
Proximity Sensors: Fully automatic canopy deployment using advanced proximity sensors, ensuring precise and safe operation.
Machine Vision: Integrated machine vision camera enables smoother auto-leveling and accurate automatic docking.
Comprehensive Data Reporting: Gather detailed reports on docking times, power connections, and environmental conditions for informed decision-making.
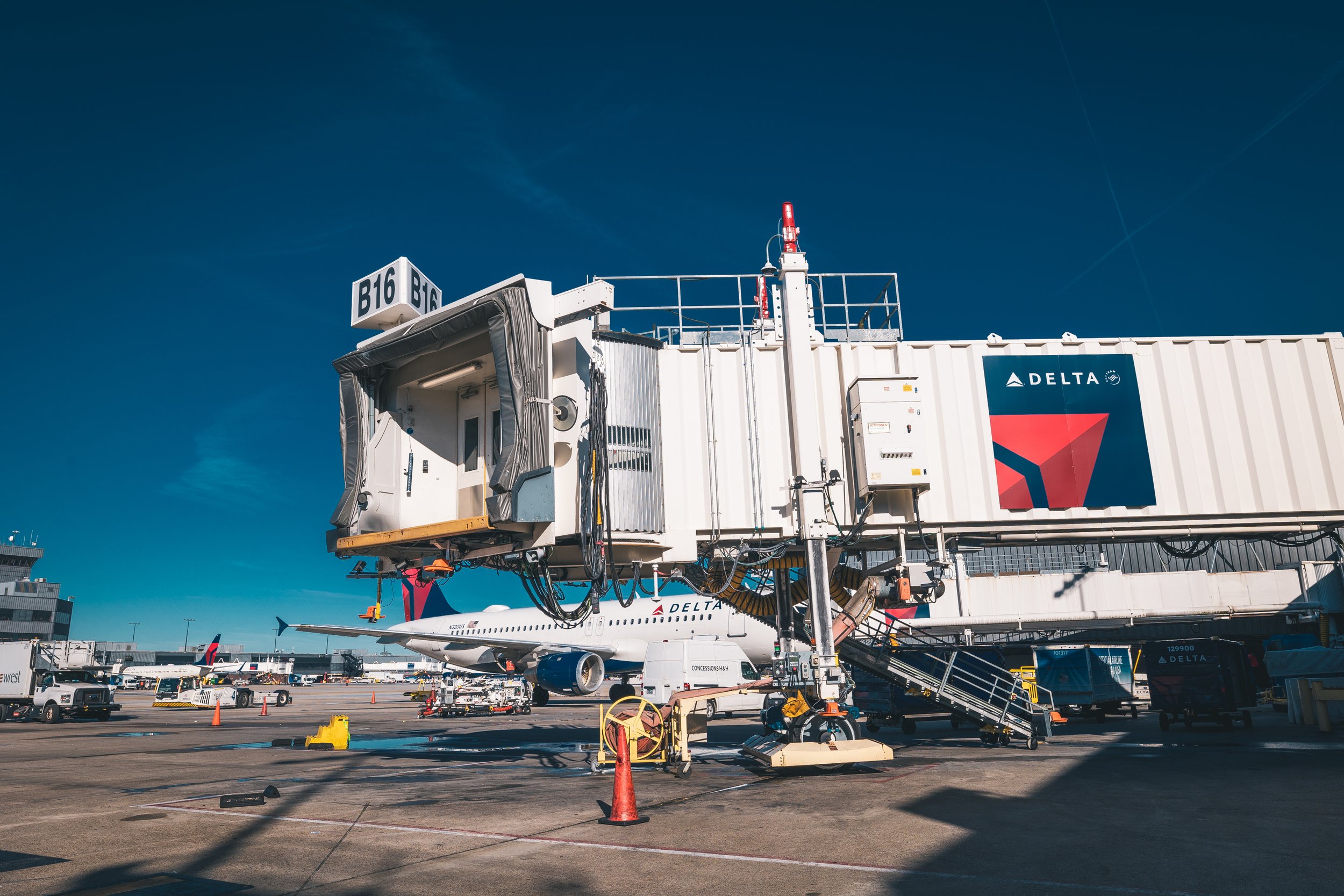
See the Bridge in Action
Watch real-world deployments of our Autonomous Passenger Boarding Bridge delivering fast, precise, hands-free docking.
PASSENGER BOARDING BRIDGE (PBB) FAQ
-
This system is currently being used at Hartfield-Jackson International Airport in Atlanta, Georgia, USA.
-
This is an upgrade to an existing system but can also be implemented as a completely new system. This depends on how much of the existing controls, such as motors, Air Handling Unit or PCAir, and 400Hz, are already integrated into the Passenger Boarding Bridge.
-
Yes, the updated PBB system can be added to most Passenger Boarding Bridges and integrates seamlessly over Ethernet or via hardwiring.
-
Yes, the updated PBB system integrates easily with APPS or SafeGate, enhancing the functionality and efficiency of the bridge.
-
The updated PBB control system features an intrusion detection system that monitors areas around the bogie wheels and stairs during motion. This protects ground crew members and equipment from potential accidents, ensuring a safer operational environment.

Autonomous Passenger Boarding Bridge Docking System
This proprietary PBB technology from CLX Engineering, significantly reduces the time required for passenger offboarding and bridge docking. In automatic mode, the bridge docks in just 45 to 48 seconds, a remarkable improvement compared to the 90 to 120 seconds typically needed for manual docking. This efficiency not only speeds up operations, reducing turnaround times for airlines, but also enhances the passenger experience by minimizing delays and ensuring a smoother transition from plane to terminal. The time saved directly translates to increased operational capacity and cost savings, making it a game-changer in the aviation industry.
PRECISION DOCKING WITH AUTOMATED CONTROL
The PBB’s Auto Docking Sequence allows for precise and efficient docking with reduced manual intervention. Once the plane parks, the operator initiates motion using two enable pushbuttons, and the PBB autonomously drives to the aircraft using preposition profiles based on plane type. With the machine vision docking camera and multiple stop sensors, the PBB ensures a fast, safe, and reliable connection, reducing docking times to as low as 45 seconds.
SEAMLESS RETRACT AND RESET OPERATIONS
After passenger boarding, the PBB can automatically return to its home stow box with the touch of a button. The system raises the auto-level wheel, retracts the canopy, and initiates the motion back to the home position. This smooth and controlled process not only ensures operational efficiency but also provides maintenance teams the ability to home all axes, maintaining long-term precision for autonomous airport solutions.
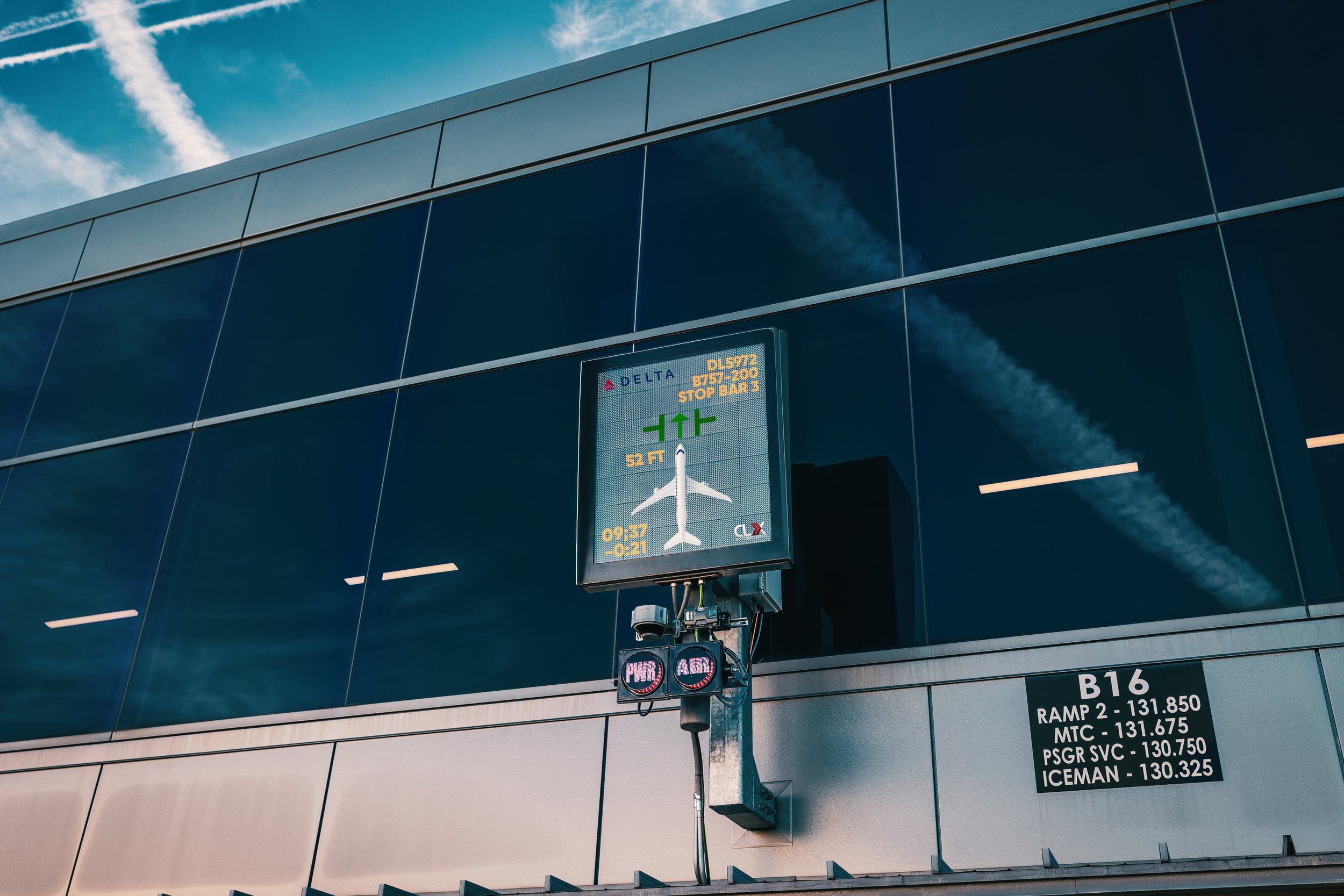
AUTOMATED PILOT PARKING SYSTEM (APPS)
Revolutionizing Gate Parking Automation
For Pilots and Airports
The Automated Pilot Parking System (APPS) is a new automation system used to remotely help guide pilots into their assigned gate during the parking process. The system is composed of multiple subsystems. Each of these subsystems works in unison to help perform, monitor, and maintain APPS. The system constantly monitoris the gate and provides video playback options when intrusions are detected. The video feed of each gate is available remotely to allow admin users to make decisions on whether an intrusion bypass is acceptable to allow the pilot to continue driving into their parking position at the gate.
HOW APPS WORKS:
APPS combines advanced technologies into a cohesive system that supports pilots, ground crews, and administrators.
1. Vision Monitoring System
Identifies aircraft type upon gate entry to confirm alignment with Tower information.
Captures real-time video for redundancy and intrusion assessment.
Configures center lines and stop bars using point-cloud modeling.
2. Laser-Based Monitoring System
Employs laser sensors to monitor gate perimeters and guide aircraft.
Calculates precise distance to the stop bar and offsets from the center line.
3. Pilot Display
Provides pilots with real-time feedback on their alignment and distance to the stop bar.
Displays gate status for ground crews, ensuring seamless communication.
4. Below Deck Groundcrew HMI
Delivers gate status updates and allows ground crews to bypass or resolve faults.
Ensures synchronized communication between ground crews and pilots.
5. Remote Maintenance Software Tool
Configures and monitors individual gates, including aircraft types and gate perimeters.
Allows remote access to ground crew functions for enhanced operational flexibility.
6. APPS Web Interface Monitoring Tool
Enables airport-wide monitoring for administrators.
Offers playback of recorded parking sequences and gate history.
Provides centralized control to update Pilot Display messages during weather disruptions or gate maintenance.
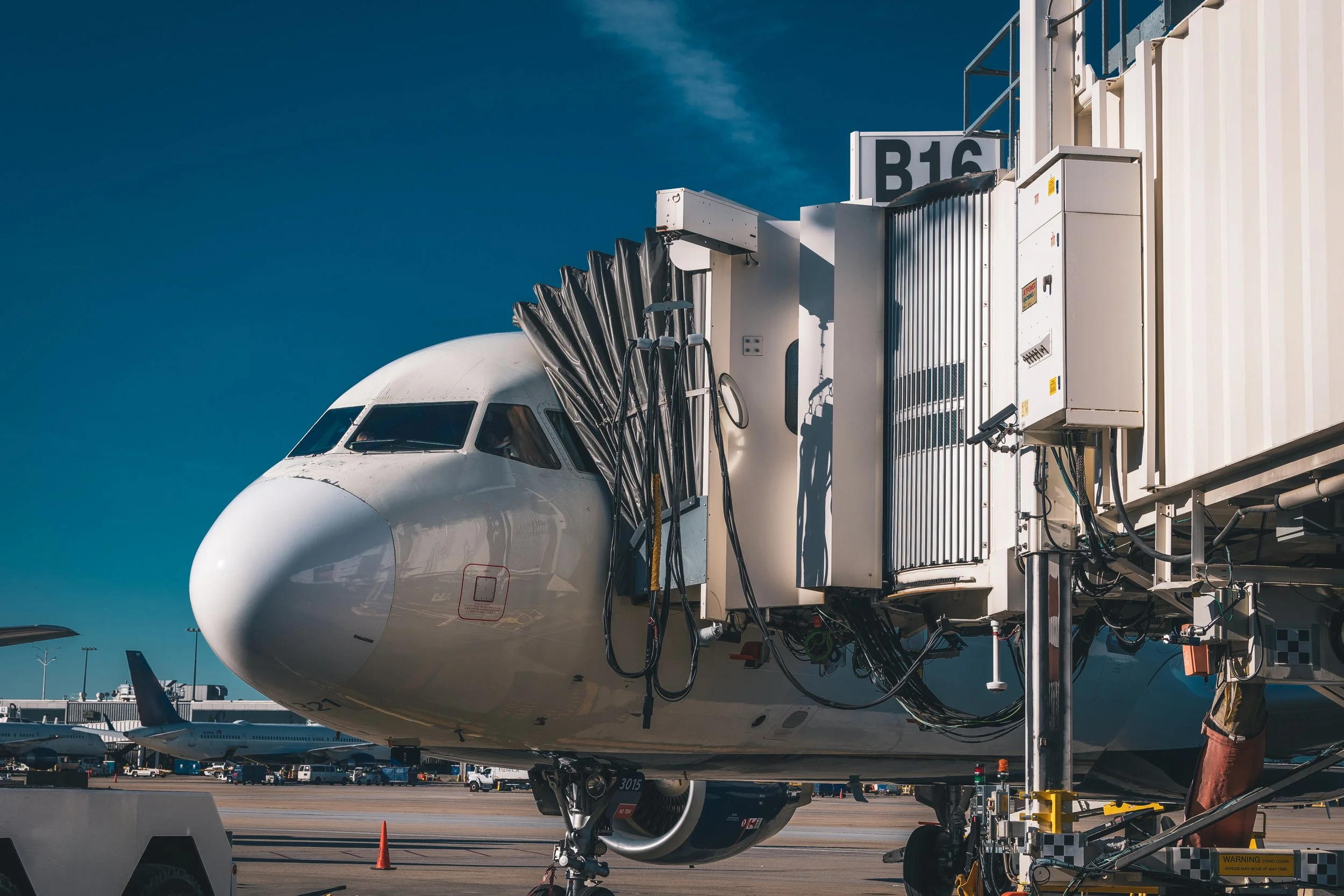
FAQ’s FOR AUTOMATED PILOT PARKING SYSTEM (APPS)
-
APPS (Automated Pilot Parking System) is an advanced automation system designed to guide pilots into their assigned gate safely and accurately during the parking process. It enhances operational efficiency by integrating multiple subsystems for real-time monitoring, precision guidance, and remote access, reducing delays and ensuring optimal safety.
-
APPS uses a combination of Vision Monitoring and Laser-Based Monitoring Systems to detect intrusions. If an intrusion is detected, the system records the event and provides video playback options. Administrators and ground crews can assess the intrusion remotely and decide whether to bypass it, allowing the pilot to continue the parking sequence.
-
Yes, APPS offers remote monitoring capabilities through its Remote Maintenance Software Tool and Web Interface Monitoring Tool. The Remote Maintenance Tool allows users to manage individual gates, while the Web Interface Tool provides airport-wide monitoring, playback of parking sequences, and access to gate history.
-
If APPS detects a fault or issue, the system alerts both the pilot (via the Pilot Display) and the ground crew (via the Below Deck Groundcrew HMI). Ground crews can clear or bypass the fault using the HMI or Remote Maintenance Tool, ensuring minimal disruption to the parking process.
-
APPS is highly adaptable, allowing users to configure center lines, stop bars, and gate perimeters for various aircraft types using the Remote Maintenance Software Tool. During inclement weather, administrators can update the verbiage on all Pilot Displays through the Web Interface Tool, ensuring clear communication tailored to the situation.
WANT TO LEARN MORE ABOUT
OUR PBB & APPS TECHNOLOGY?
Access the guide for more information.